Edit..... I added 2 final pics in this post........................
I bought a .750 gun drill on Ebay for $10.
It is 36 inches long but that works out ok on a hightower deluxe. I have lots of room. I modified this one the easy way.
I tapped the coolant hole in the back of the drill for 3/8-16 and made an aluminum adapter and tapped that. I screwed them together and turned the adapter using the drill as a mandrel.
I came with one insert that will probably last until I die.
I bought a .750 gun drill on Ebay for $10.
It is 36 inches long but that works out ok on a hightower deluxe. I have lots of room. I modified this one the easy way.
I tapped the coolant hole in the back of the drill for 3/8-16 and made an aluminum adapter and tapped that. I screwed them together and turned the adapter using the drill as a mandrel.
I came with one insert that will probably last until I die.
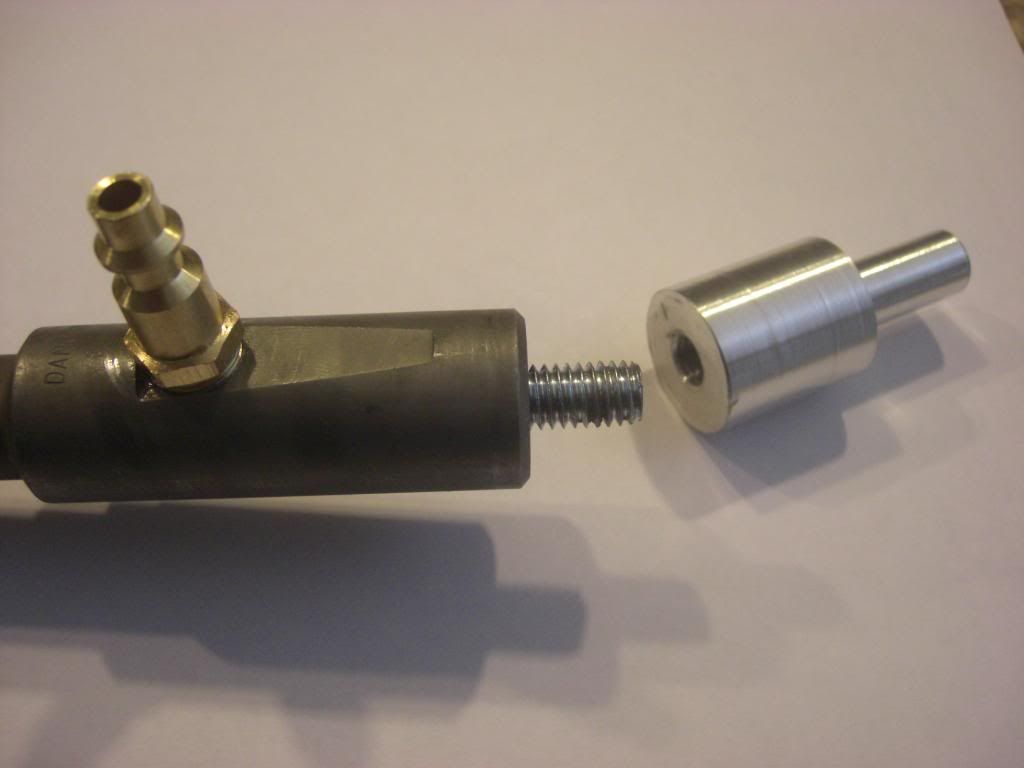
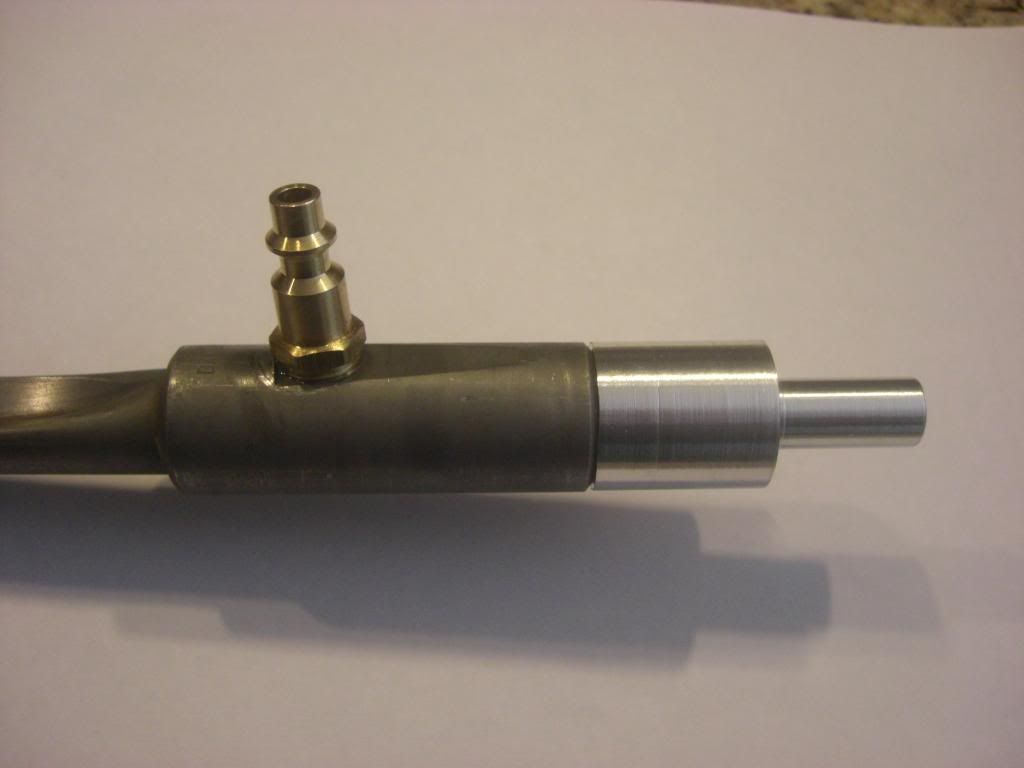
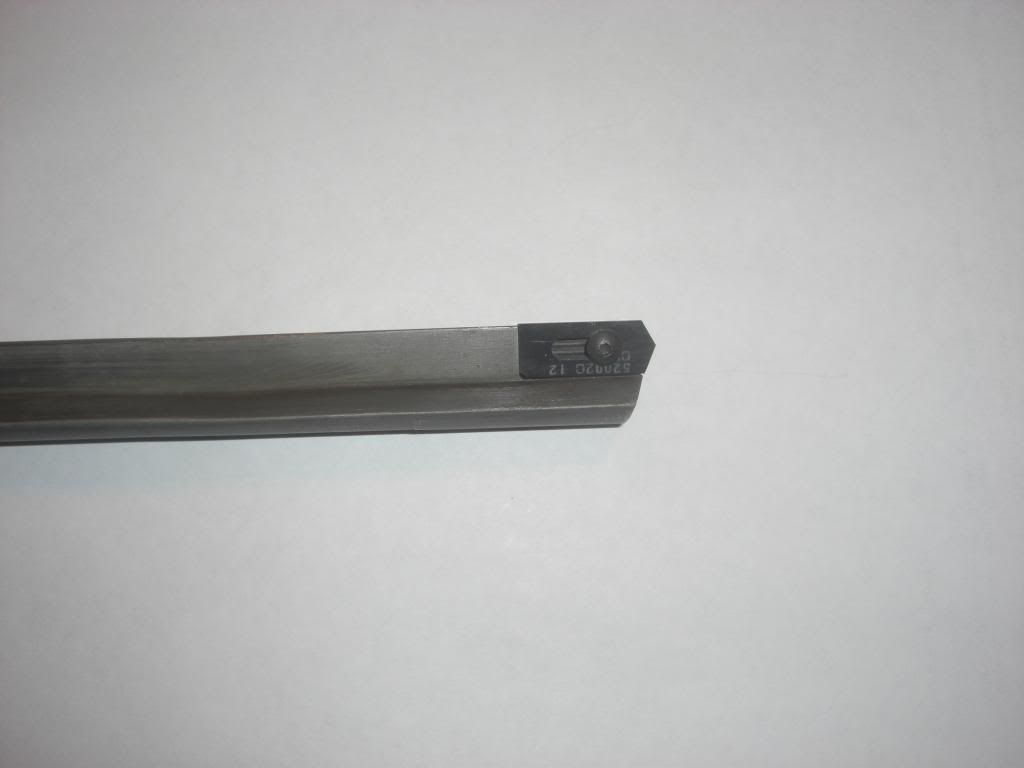
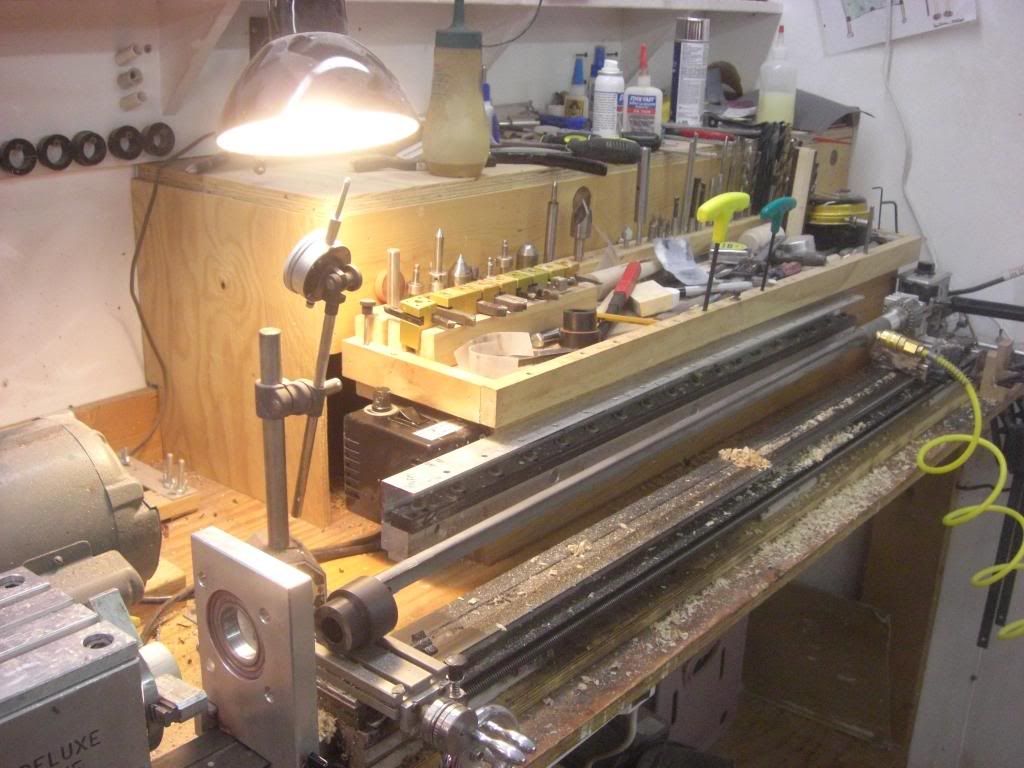
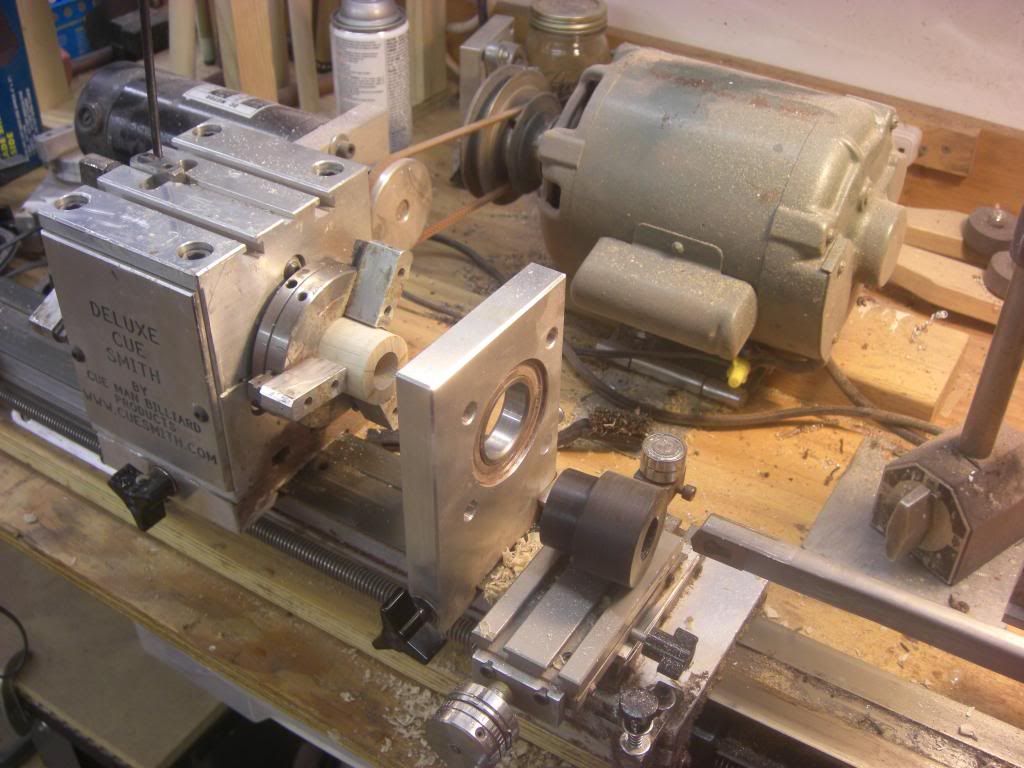
Last edited: