I core every thing on the cue at .750. I bought mt gun drill about 15 years ago and was one of the first to core their cues. When I ordered the drill it never dawned on me that the coring dowels would have to be a little smaller than .750 or I would have ordered the bit a little larger so that standard size phenolic and rings could easily be used. I can think of no reason why any builder would want to design a joint as small as .800 so unless your prong warps right at the joint why worry that the cue has been bored at .780. You just need to be sure that your dowel has good centers before use as a core.
Dick
Hi,
Ditto .750. I turn my dowels to .737 for gorilla glue expansion. I drill my ring billets out to .740 so my ring geometry does not get eccentric to the points in the A-Joint area, nice close ID fit.
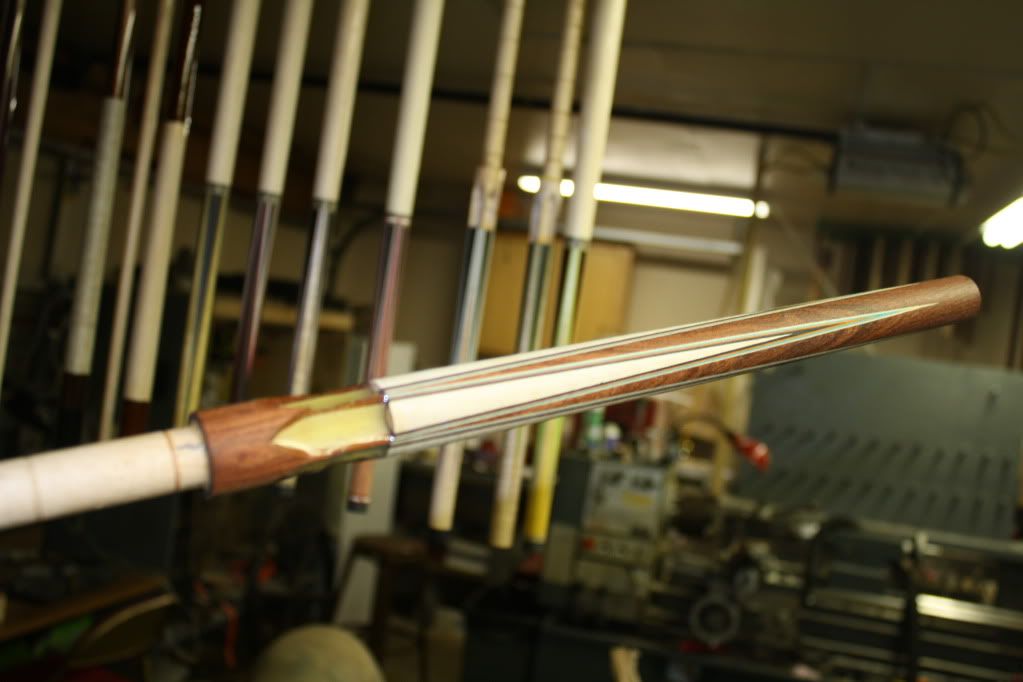
Decor Rings must have a close ID to dowel fit or ring geometry can get out of alignment on the A-Axis when you view your completed cue.. This fit concentricity is something you must pay close attention to when full coring. It is not like cutting a tenon and test fitting your rings for the close fit. The dowel can not be too close of a fit or you will piston out your glue during install. This is why GG Glues is perfect for coreing as opposed to using epoxy that does not expand by 5 times the volume. No buzzing with GG guaranteed! JMO
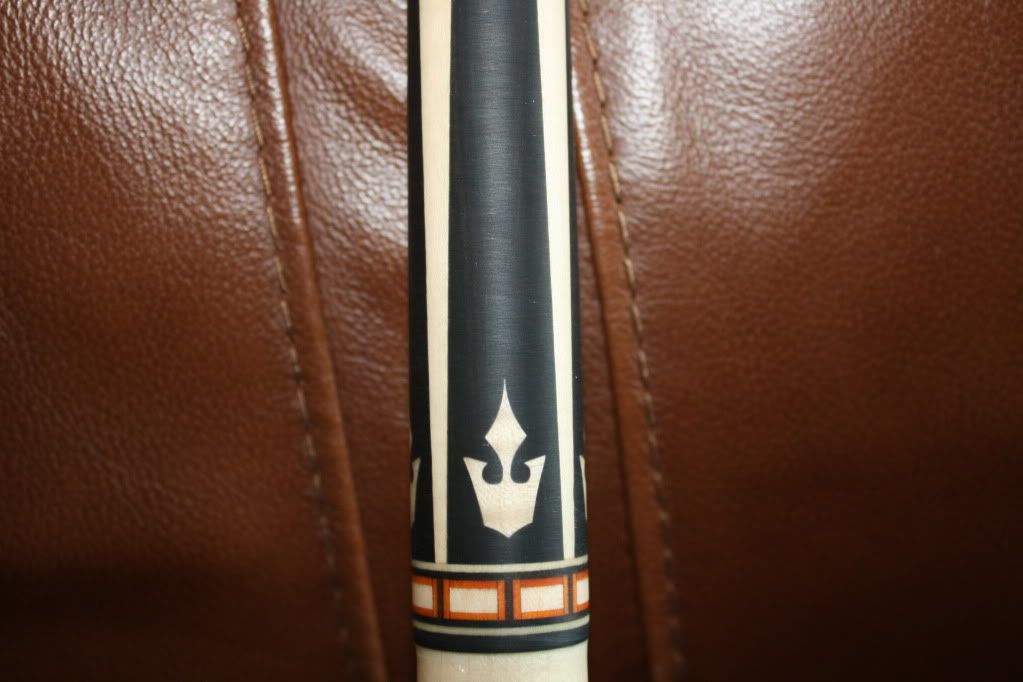
Last edited: