the original post asked about about g10 pins
http://forums.azbilliards.com/showthread.php?t=301039
i had posted this - the g10 pin is a premium pin, i personally would leave it alone. i've never seen them coming apart but they do have sharper crowns than the metal. the pin is used for less weight and to protect the butt and shaft if it were to fall over....the pin would break instead of putting stress on the joint and possibly splitting the shaft or screwing up the collar. you just drill out the glass pin parts that are broke and replace. if you lightly buff the pin, you should not have any problems.
got an interesting response - Perhaps I'm totally wrong, but...
Pins are made out of G10 because it's light yet very strong. I highly doubt "ease of replacement" factored into the picture. Yes, G10 pins are far easier to machine out than a metal pin. Then again, when replacing a metal pin it's much easier to heat the pin to break down the glue.
As far as the G10 pin "protecting" the joint during a fall... Huh? Have you ever tried to break a G10 pin? Clamp one in a vise and whack it with a hammer. I guarantee you they're stronger than you're describing. If an "accident" occurs that breaks the G10 pin, I'd be willing to bet there's going to be more repairs needed to the cue than just a new pin.
The typical "problem" with G10 pins is this: G10 pins can only effectively be made into large threaded pins (3/8-10, Radial, etc.) which screw into wooden threads in the shaft. The raw G10 material is quite abrasive and over time it will grind down the inner surface of the wooden threads causing the joint to loosen up. Some remedies are wax or thin CA on the G10 threads.
G10 pins are no more "premium" than stainless, brass, or aluminum.
it inspired this experiment - g10 threaded into scrap shaft. put in vise and with just a light push on the shaft (about 6" from the joint collar) i get this.
now about that guarantee......
http://forums.azbilliards.com/showthread.php?t=301039
i had posted this - the g10 pin is a premium pin, i personally would leave it alone. i've never seen them coming apart but they do have sharper crowns than the metal. the pin is used for less weight and to protect the butt and shaft if it were to fall over....the pin would break instead of putting stress on the joint and possibly splitting the shaft or screwing up the collar. you just drill out the glass pin parts that are broke and replace. if you lightly buff the pin, you should not have any problems.
got an interesting response - Perhaps I'm totally wrong, but...
Pins are made out of G10 because it's light yet very strong. I highly doubt "ease of replacement" factored into the picture. Yes, G10 pins are far easier to machine out than a metal pin. Then again, when replacing a metal pin it's much easier to heat the pin to break down the glue.
As far as the G10 pin "protecting" the joint during a fall... Huh? Have you ever tried to break a G10 pin? Clamp one in a vise and whack it with a hammer. I guarantee you they're stronger than you're describing. If an "accident" occurs that breaks the G10 pin, I'd be willing to bet there's going to be more repairs needed to the cue than just a new pin.
The typical "problem" with G10 pins is this: G10 pins can only effectively be made into large threaded pins (3/8-10, Radial, etc.) which screw into wooden threads in the shaft. The raw G10 material is quite abrasive and over time it will grind down the inner surface of the wooden threads causing the joint to loosen up. Some remedies are wax or thin CA on the G10 threads.
G10 pins are no more "premium" than stainless, brass, or aluminum.
it inspired this experiment - g10 threaded into scrap shaft. put in vise and with just a light push on the shaft (about 6" from the joint collar) i get this.

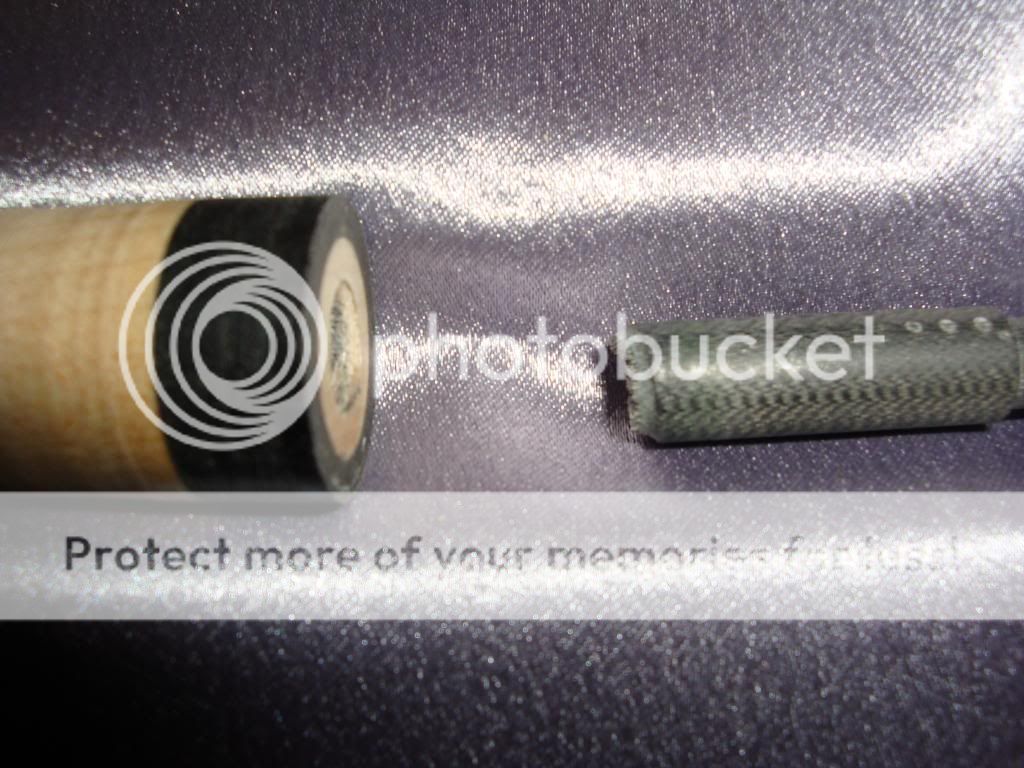
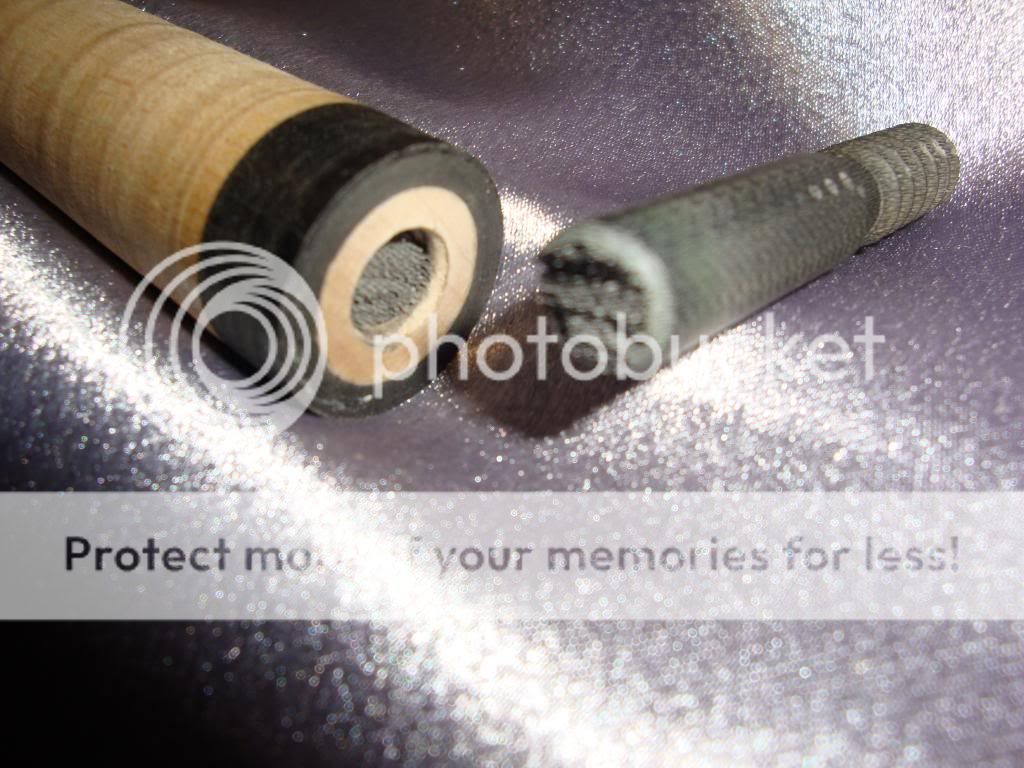
now about that guarantee......